Line Balancing Optimization in Industry 4.0: Turning Challenges into Opportunities
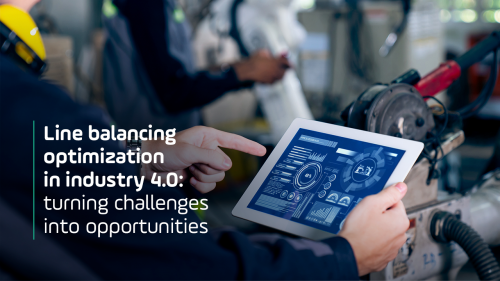
Have you ever wondered how large factories keep their production lines running harmoniously? Or why, even with advanced technology, inefficiencies still impact the bottom line?
In the fast-paced world of modern manufacturing, every second counts. As we move deeper into the era of Industry 4.0, factories aim not only to produce more — but to produce better, with less waste and greater predictability. This is where the concept of Line Balancing Optimization (LBO) comes into play — an approach that’s revolutionizing the way production lines operate.
In this article, we’ll explore how integrating smart technologies with line-balancing strategies creates a new paradigm in industrial production — where machines work in perfect harmony, like a well-rehearsed orchestra, dynamically responding to changes and challenges in the production environment.
1. Predictability and Adaptability: The Path to Efficiency
At the core of Industry 4.0 are two fundamental pillars for achieving operational excellence: predictability and adaptability. According to the Industrie 4.0 Maturity Index by Acatech (German Academy of Science and Engineering), companies with advanced capabilities in these areas can reduce operating costs by up to 30% and increase overall productivity by 25%.
The ability to anticipate problems before they occur and adjust operations in real-time radically changes how we handle production challenges. When operators and managers have access to precise, real-time information, decision-making becomes faster and significantly more effective.
The Data Revolution in Manufacturing
With the implementation of strategically placed IoT sensors and real-time data analytics systems, modern factories can:
- Identify machine behavior patterns, detecting subtle anomalies before they escalate into major failures. McKinsey & Company reports that data-driven predictive maintenance can reduce unplanned downtime by up to 50% and extend equipment lifespan by up to 40%.
- Proactively adjust machine speeds, eliminating bottlenecks before they even appear. This preventive approach is essential for maintaining continuous production flow.
- Improve production planning using predictive scenarios, factoring in variables like raw material availability and environmental conditions affecting equipment performance.
The Customization Challenge
Every industrial plant is unique — with its infrastructure, technology level, workflows, and culture. This means the journey toward predictability and adaptability must be tailored with customized solutions.
This is where Line Balancing Optimization (LBO) becomes essential. It’s not just a system, but an operational philosophy that aims for perfect harmony across production line components.
The Five-Level Structure of LBO
LBO is structured across five progressive control levels, each building upon the previous:
- Equipment Assessment – Continuous monitoring through sensors tracking key parameters (temperature, vibration, pressure) enables early deviation detection and predictive maintenance. The Fraunhofer Institute states predictive maintenance can cut maintenance costs by up to 30%.
- Speed Adjustment – Each line segment operates at its optimal speed, accounting for real conditions and product quality goals. Dynamic optimization eliminates both idle time and overload.
- Conveyor and Accumulation Optimization – Smart flow management between workstations uses prediction algorithms to regulate speed and maintain flow. The University of Stuttgart found this can increase conveyor efficiency by up to 35%.
- Cascade Control – Synchronized restart protocols after stoppages ensure operations resume smoothly and in sequence, reducing downtime by up to 40% (ABB data).
- Linked Speed Auto-Control – The most advanced level, where the line behaves as a single organism. Machine learning algorithms dynamically adjust operations based on sensor feedback.
The Silent Impact of Micro-Stoppages
One of the biggest efficiency killers in the industry is micro-stoppages — brief interruptions that seem minor but accumulate into substantial losses. According to BCG, micro-stoppages can lower Overall Equipment Effectiveness (OEE) by 10–15% even in efficient plants.
They:
- Distract operators from high-value tasks
- Create a reactive, high-stress environment
- Undermine proactive planning
The Hidden Costs of Micro-Stoppages
- Production losses: Small pauses across shifts mean lost capacity. Deloitte notes a 1% uptime improvement can lead to millions in annual revenue gains.
- Material waste: Flow interruptions often spoil partially processed goods, raising costs and environmental impact. The World Business Council for Sustainable Development reports up to 20% waste reduction through process optimization.
- Revenue loss: Downtime means lost sales. HBR found that operational efficiency often defines market leaders.
- Increased risks: Frequent manual interventions raise the risk of accidents. The ILO says automation of risky tasks can reduce incidents by up to 25%.
2. Success Case: Bottling Line Modulation
A powerful example of LBO in Industry 4.0 is the modulation of bottling lines — a solution that demonstrates how smart sensors, real-time data analytics, and advanced automation can transform problematic operations.
How It Works
The system acts like a digital conductor. Using the OPC UA protocol (recognized as an Industry 4.0 standard by the OPC Foundation), it integrates with machines regardless of brand or age.
It continuously monitors:
- Machine Status: Real-time status (operating, idle, faulty) enables fast intervention.
- Line Speed: AI algorithms calculate ideal speeds for each segment. The Technical University of Munich reports up to 18% productivity gains.
- Transport Accumulation: Monitors flow to avoid congestion. Gartner shows IoT flow control systems reduce unplanned stoppages by up to 30%.
Real-Time Efficiency
Every 2–4 seconds, the system:
- Captures data from dozens/hundreds of points
- Analyzes via optimization algorithms
- Calculates and implements adjustments — all autonomously
This operational visibility reflects the Acatech Maturity Index principle: data-driven decision-making.
Quantified Benefits
- Operational Predictability: Less uncertainty, better planning. PwC says this can cut safety stock by 30%.
- Quality Consistency: Stable speeds ensure product uniformity. The ASQ notes that a 1% quality boost cuts 2–3% of total operating costs.
- Extended Equipment Life: Smooth operations reduce mechanical wear. SKF studies show critical components can last 50% longer.
- Drastic Reduction in Micro-Stoppages: MESA reports up to 80% fewer micro-stoppages with smart speed control.
- Improved Safety: Fewer manual interventions lower accident risk. NFPA says automated systems can reduce exposure by 65%.
- Critical Process Automation: Rebooting after stoppages becomes standardized and fast. ISA data shows up to 45% recovery time reduction.
- Financial Impact: Aberdeen Group found that automation leaders have 7% higher operating margins than laggards.
3. How Mouts Can Support Your Industry 4.0 Journey
Many companies hesitate to digitize because they believe Industry 4.0 requires a full-scale overhaul. This “all-or-nothing” mindset leads to analysis paralysis or failed mega-projects.
The truth is: The Industry 4.0 should be incremental, with quick wins that show value and build momentum. Solutions like bottling line modulation are exactly that — high-impact implementations that don't disrupt existing operations.
Our Collaborative Approach
At Mouts, we believe each business has its rhythm and goals. Our cross-functional teams work alongside yours to:
- Diagnose operational pain points with precision
- Design custom solutions that integrate with your current setup
- Deploy incrementally with agile methods and continuous feedback
- Empower your teams to use and evolve the solution
As the World Economic Forum emphasizes, competitive advantage lies not just in adopting tech — but in aligning it with your strategy and culture.
Conclusion: Let Mouts Transform Your Production
Line Balancing Optimization is more than just tech — it's a shift in how we approach industrial efficiency. In Industry 4.0, operational excellence is about intelligence, flexibility, and resilience.
That’s where Mouts makes the difference.
Talk to our team today and ensure your operation doesn’t get left behind. The digital transformation journey is ongoing — and the sooner you start, the bigger your edge.
Related news
Innovation, the global market and divers topics about the technology universe are currently available on our blog.
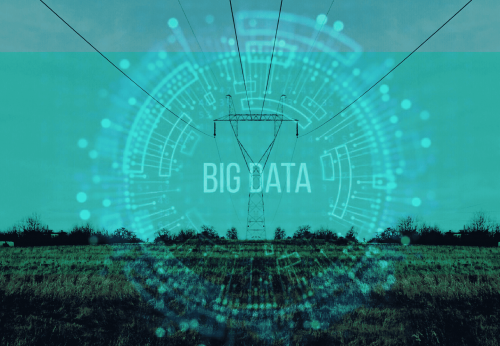
Big Data in energy: how to manage data in the energy sector?
The energy sector is one of the fundamental pillars of the global economy, driving everything from large industries to domestic consumption. With the advancement of digital technologies, the amount of data generated in this sector has increased exponentially, making Big Data an essential tool for companies seeking to stand out in a competitive market. But how to collect and analyze this data effectively? And what are the benefits of a well-done analysis?
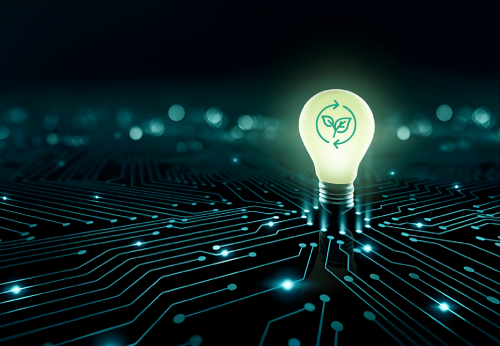
Energy and sustainability: 3 innovative technologies in the energy sector
Sustainability has become a central issue in the energy sector, driven by the need to reduce environmental impact, ensure energy security and meet growing demands for cleaner energy sources. With increasing pressure to reduce carbon emissions and adopt more sustainable practices, the sector faces significant challenges, but also promising opportunities.
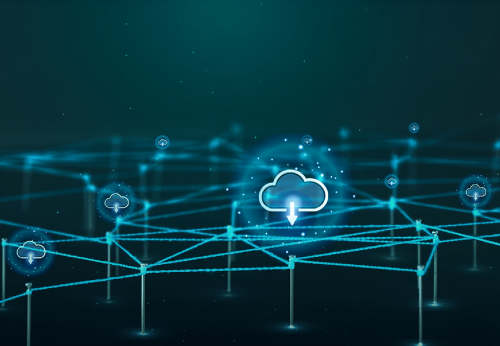
Why is cloud migration important for the energy sector?
Energy market professionals can already see that the sector is undergoing a significant transformation, driven by the need for greater efficiency, sustainability, and innovation. Amid these changes, cloud migration has stood out as one of the main strategies for companies looking to optimize their operations, reduce costs and improve collaboration.